Revon Mobility Manufactures Interior Door and Console Parts of Its Electric Vehicle
with +90 3D Digital Factory!
Revon Mobility Optimizes EV Design with Additive Manufacturing!
Revon Mobility, a manufacturer of 100% electric transport vehicles, chose Additive Manufacturing Technology to finalize the design of its vehicle components. The cost and time constraints of traditional methods played a significant role in the company’s decision to adopt this innovative approach. By leveraging Additive Manufacturing Technology, the company minimized prototyping costs while achieving the final design quickly and efficiently.
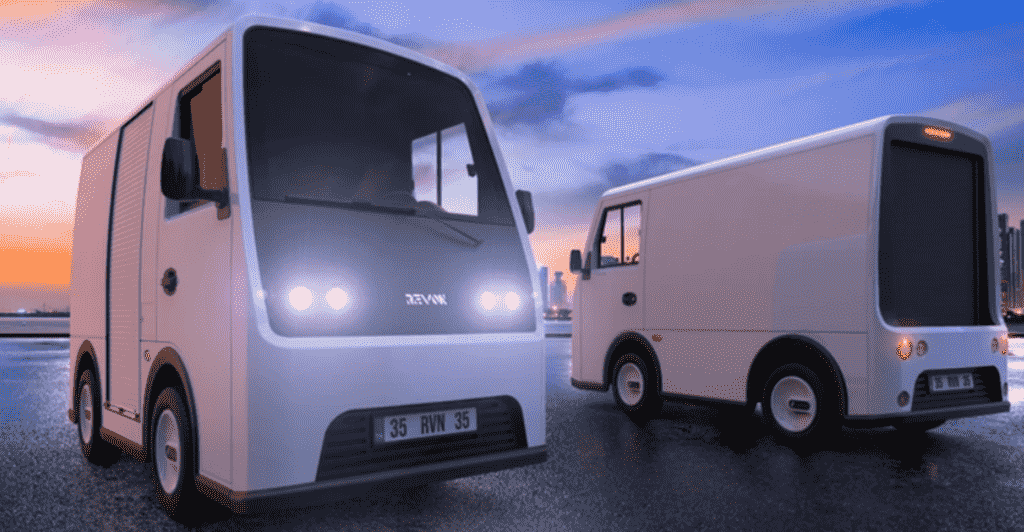
Yarkın Muslu describes his experiences with +90 3D DIGITAL FACTORY
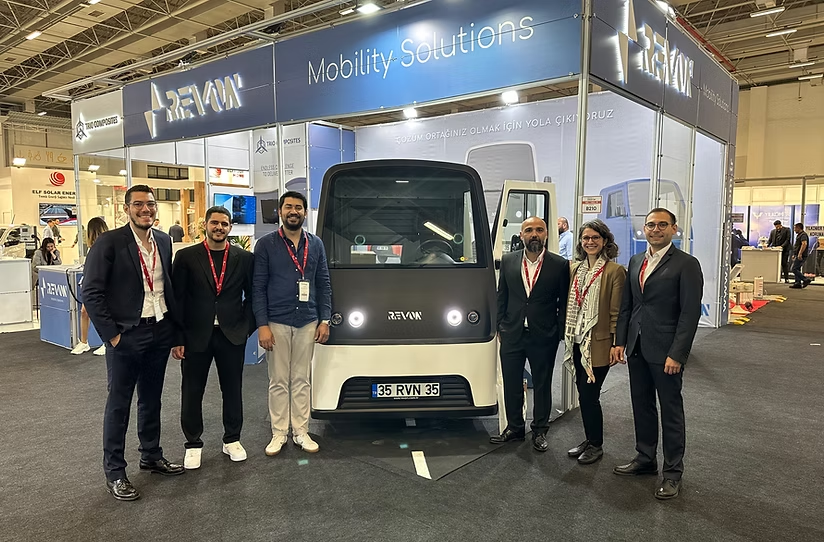
Why +90 3D Digital Factory?
“The collaboration with +90 3D Digital Factory has been highly beneficial to our vehicle’s prototyping processes. This partnership enabled Revon Mobility to refine every detail of the vehicle both aesthetically and functionally to achieve perfection.”
“Thanks to Additive Manufacturing Technologies, we were able to rapidly implement design modifications in critical areas of our vehicle’s cabin, such as the console, additional components on the console and interior door panels. Compared to traditional manufacturing methods, we achieved these changes at a lower cost. This accelerated our product development process and increased our efficiency. Moreover, this technological approach allowed us to obtain not only prototypes but also final product-quality parts.”
Technologies and Materials
Revon Mobility preferred ASA material, using the Stratasys F770 3D printer, which has UV resistance and high printing volume, in the production of door interior parts with large surface area. Smaller and more complex console and detail parts were produced using SAF (Selective Absorption Fusion) technology with PA11 material. Additionally, for large-volume parts, composite mold services were utilized to accelerate the molding process and achieve cost advantages.
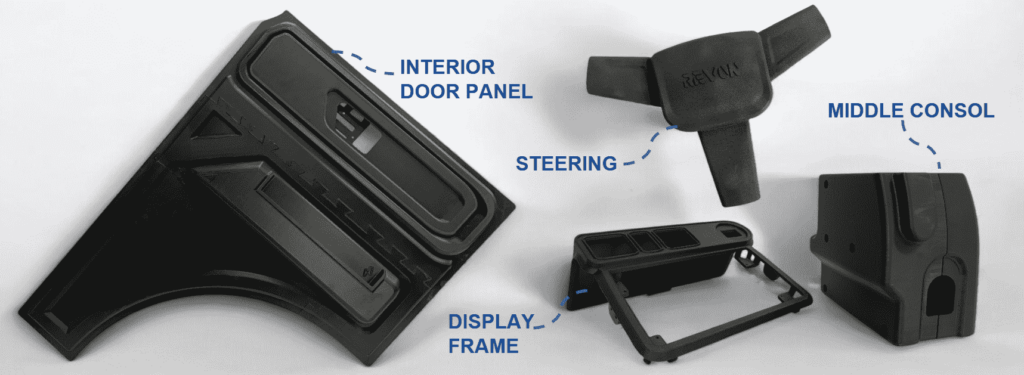
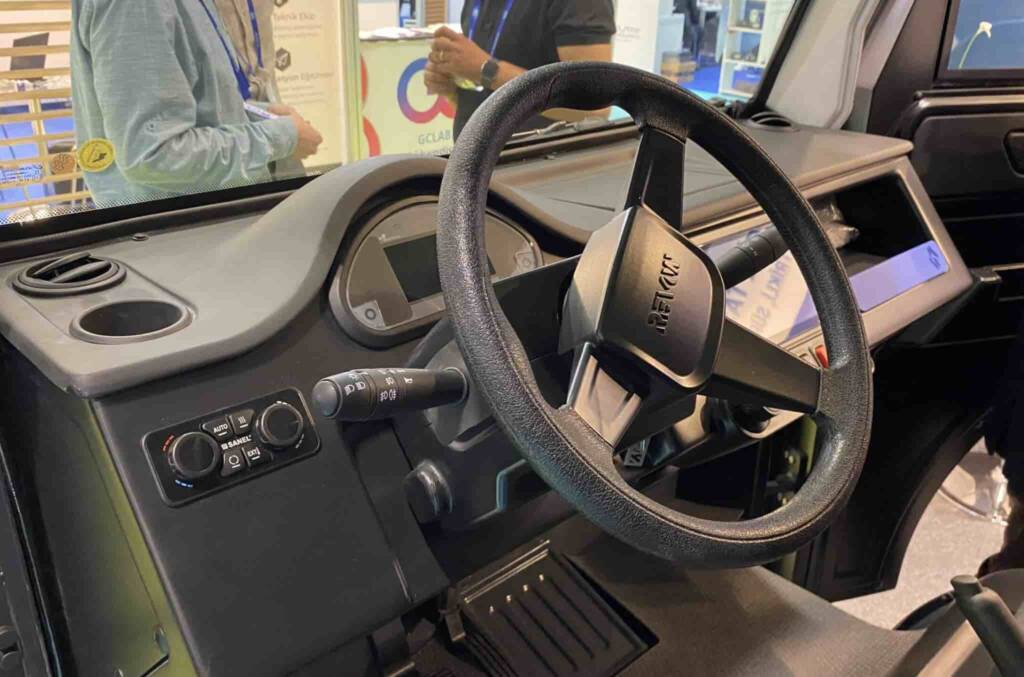
Would you recommend
+90 3D DIGITAL FACTORY?
“This collaboration was more than just a manufacturing process. Revon Mobility and +90 3D Digital Factory worked together to shape the future of electric transportation vehicles. The final products not only reflected Revon Mobility’s vision in terms of aesthetics and functionality but also reaffirmed +90 3D Digital Factory’s expertise in the industry.”
“Throughout our project, +90 3D Digital Factory provided us with confidence through their solution-oriented approach, continuous support from their expert team, and high-quality standards maintained at every stage. For these reasons, we can wholeheartedly recommend +90 3D Digital Factory to our colleagues and business partners.”