OUR QUALITY SYSTEM
Since our company was founded, we have been looking for and implementing ways to continuously improve our quality. With each passing minute, technology develops at an inevitable pace and the needs and expectations of our customers increase. We are constantly improving our knowledge, processes and services to deliver higher quality in every project we undertake. As a pioneer and leader in the industry, we have built an international reputation that we strive to maintain and develop with the advantage of having more than 15 years of experience.
ISO 9001:2015
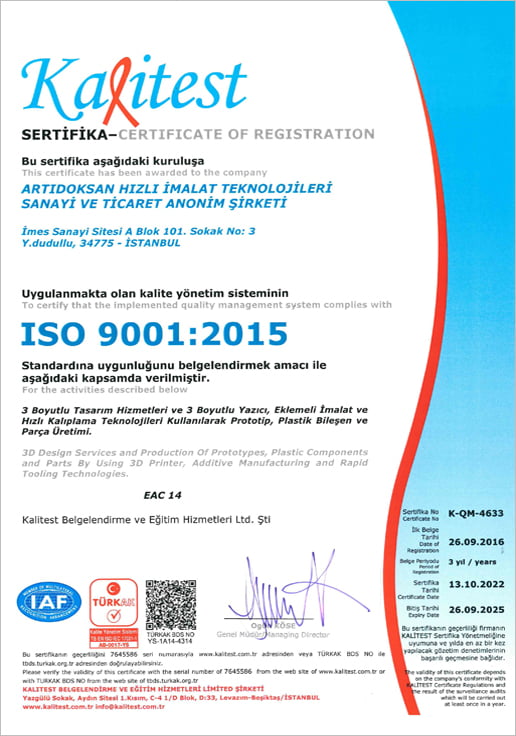
AS 9100
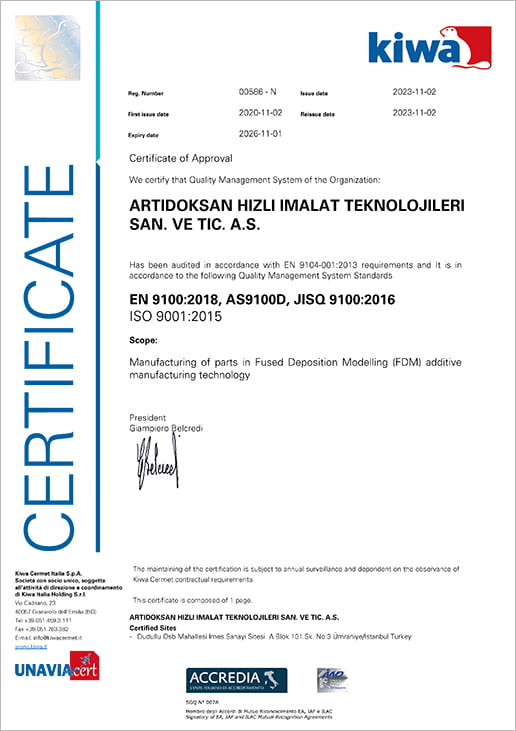
EYDEP
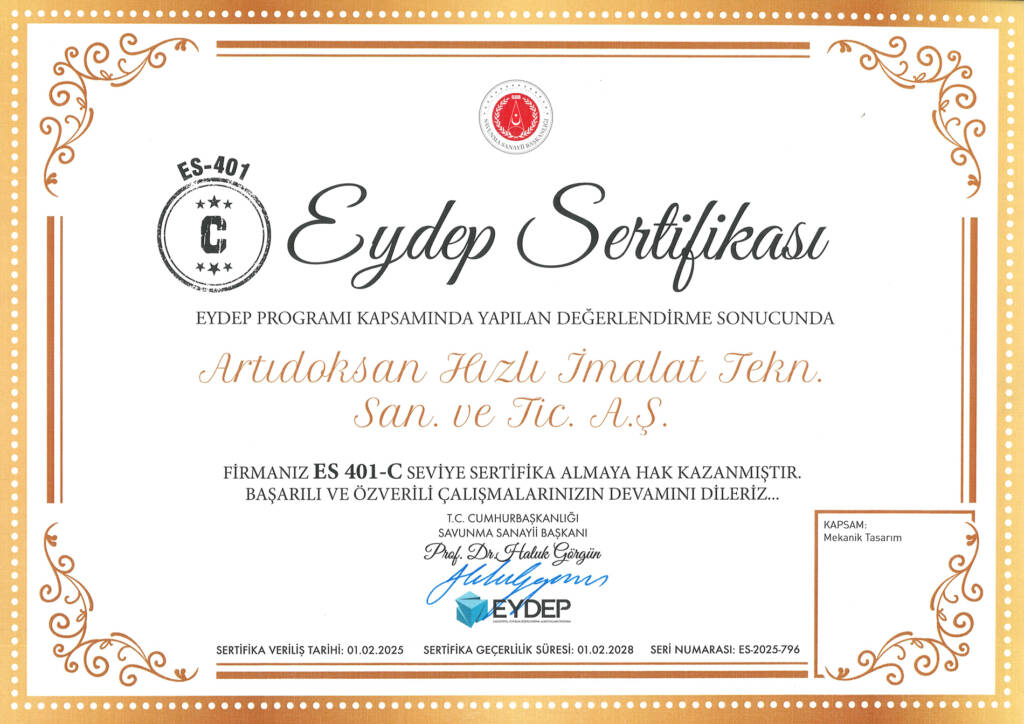
To ensure customer satisfaction by understanding customer expectations correctly, providing quality products and services to the customer on time; to improve the customer and the company by taking all necessary measures in accordance with the principles of transparency, impartiality, confidentiality, accessibility, integrity, equality and sensitivity by objectively evaluating customer feedback.
To ensure the adoption of the quality management system and to continuously increase its effectiveness by prioritizing the understanding of quality service, to comply with the applicable requirements.
To increase communication, harmony and cooperation among all stakeholders (employees, customers, partners and suppliers) to ensure that company goals and objectives are achieved efficiently.
To be a continuously developing organization with information and technology based approaches by keeping the team spirit at the highest level.
To ensure absolute compliance with occupational health and safety principles by taking human factors as a basis in all activities of the company.
To ensure that environmental protection and development awareness is adopted by all employees.
Supporting all personnel with training, ensuring that they work in line with standard work steps and company procedures, and fulfilling customer and authority applicable rules.
Ensure that all staff cooperate with quality controllers of the authority, company and customers.
To encourage the reporting of relevant improvement opportunities to support continuous improvement.
To be able to adapt quickly and flexibly to new requirements arising from national or global changes.
AS9100 (BS EN 9100) is a quality and risk management standard for the aerospace industry. AS 9100 Aviation, Space, Defense Quality Management System Standard is an international quality management system created by adding additional requirements specific to the aviation sector in addition to the ISO 9001 Standard. By certifying the AS/EN 9100 standard, companies that design, develop, manufacture and provide sales services for defense, space and aviation products ensure that the expectations of their business partners and customers will be met at the highest level.
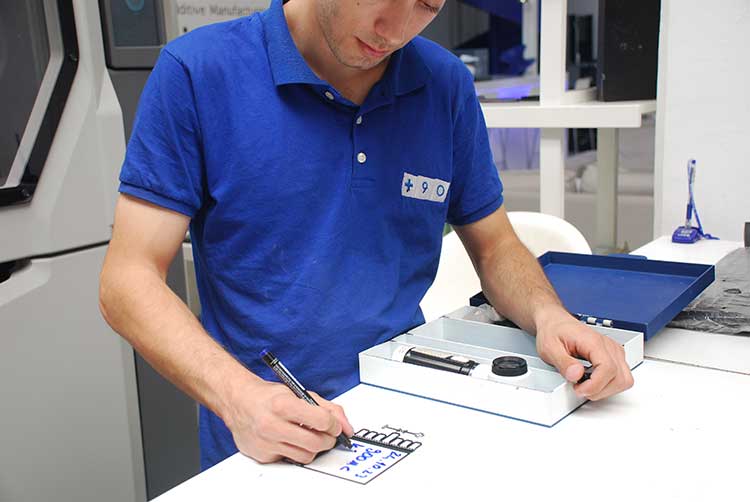
OUR LEAN +90 3D DIGITAL FACTORY
We ensure our understanding of quality, which is an indispensable condition for customer satisfaction, and its sustainability with the philosophy of “lean management”. Our goal in lean management philosophy is not only to implement lean management with a quality team, but also to ensure the adoption of continuous improvement philosophy in all units of our company and to continuously increase customer satisfaction with lean management principles.