Sand Casting
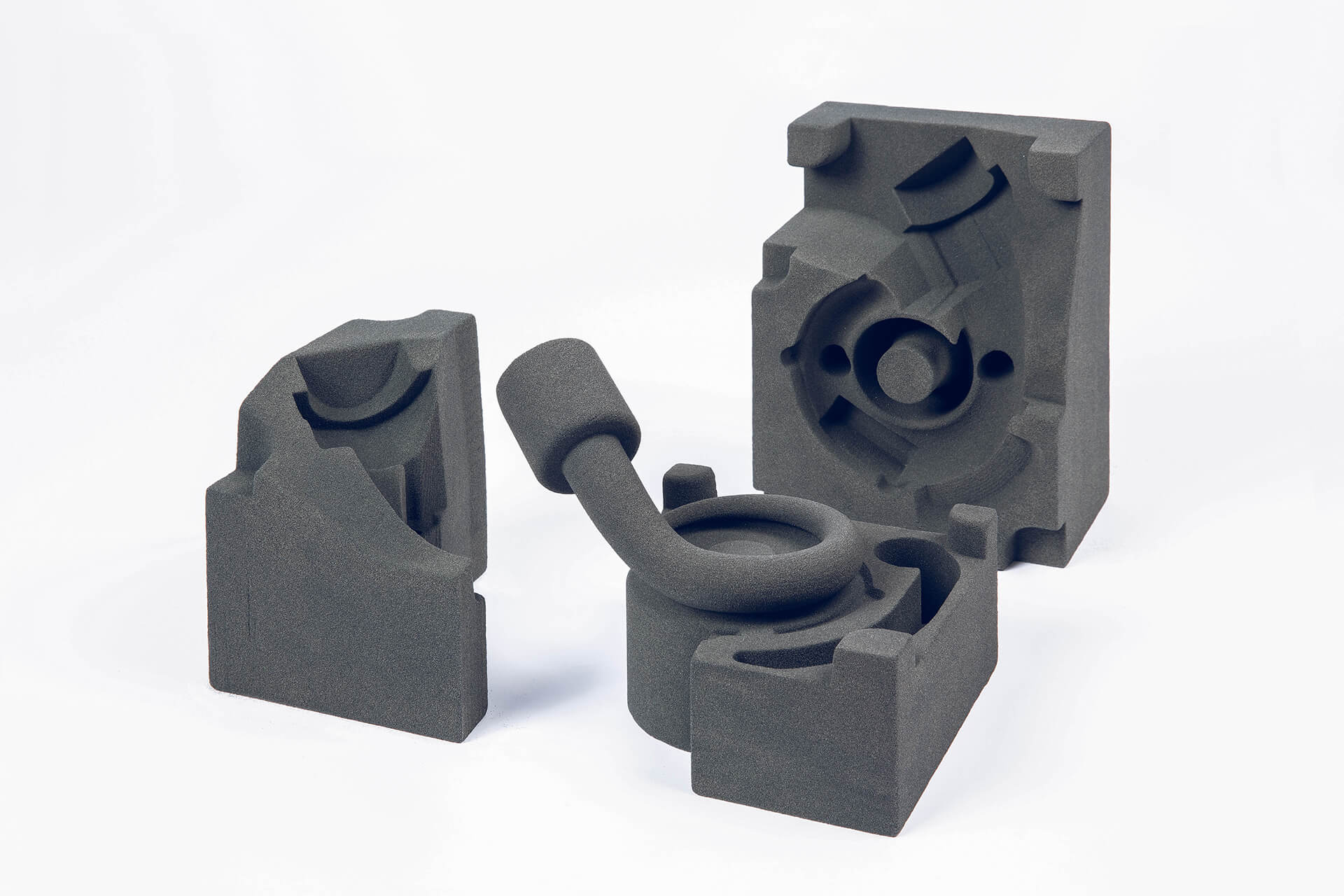
With 3D printing, you can save time and money compared to traditional production. Compared to traditional production, 3D printing offers a clear cost advantage. By choosing 3D printing instead of traditional manufacturing methods, you can reduce your costs by up to ¼.
With 3D printing, you can significantly shorten your mold and core production process while saving costs. Since only one CAD file is sufficient to produce sand molds and cores on 3D printers, you can carry out your production without expensive tooling investments.
Contact Us for Your Offer Requests and Questions!
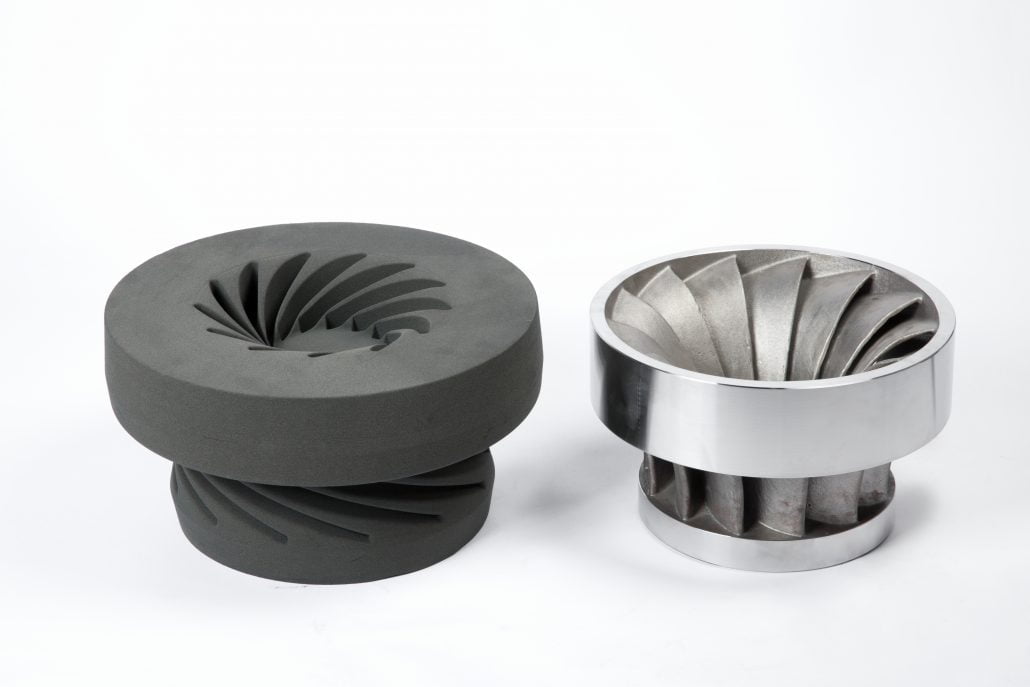
ECONOMIC SOLUTION FROM PROTOTYPES TO LOW VOLUME MANUFACTURING
Thanks to the production of sand molds and cores without tools, you can make your manufacturing from single parts to small series in an economical way. Unlike traditional production methods, the complexity of your molds and cores has almost no importance in 3D printing. You can easily produce complex geometries with 3D printers.
The advantages of 3D printing are particularly pronounced in situations such as sand core manufacturing for turbine wheels. In the traditional production method, the individual core parts of the turbine blades must be mounted to the core in a hard way. In 3D printing, the entire turbine core can be produced in one piece. This significantly shortens the entire production process since the core assembly step is eliminated. Thus, up to 75% savings can be achieved in series with fewer quantities.
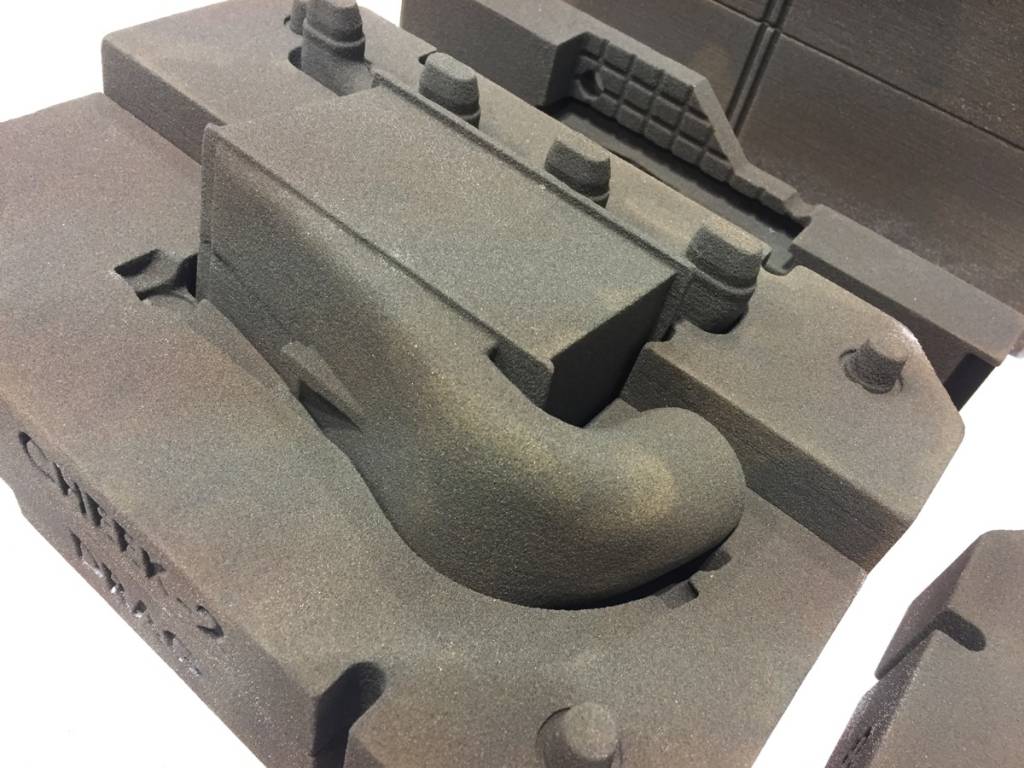
TIME IS MONEY
Short delivery times and a high degree of flexibility play an important role in fullfilling many of your needs. With the Voxeljet 3D printing process, you can produce your sand molds and cores in just a few days. This way you can save a few weeks from time compared to traditional production methods. Also, you don’t have to worry about things like opposite angles or de-mold angles. You can increase your flexibility in many ways.
Various molding devices that cannot be produced as a single piece can also be easily manufactured by 3D printing. You can also make changes to the part quickly and easily. 3D printing significantly reduces the time and money spent on mold and core production, while allowing complex geometries to be manufactured easily. 3D printing and traditional production can be combined optionally.
FROM 3D PRINTING CORE TO CASTING PART
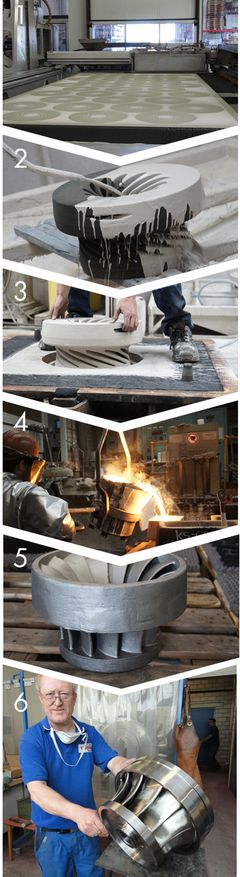
1- 3D PRINT
Sand molds or cores are manufactured by additive manufacturing method. The powder laying unit distributes the powdered material in a very thin layer throughout the entire building area. The print head then applies adhesive to the areas where the part will be produced. These two steps continue repeatedly until the entire piece is produced. After the part production is completed, the dust material is removed from the part.
2- PAINTING
Like traditional sand molding, the 3D printing core is suitable for painting. It has high thermal resistance with painting.
3- MOLD CORE INSTALLATION
The 3D printed sand core is placed in a conventionally produced mold. Conventional production methods and 3D printing can often be combined on demand.
4- CASTING
Casting of turbine wheel is done. All commonly used alloys can be cast into 3D printed molds or cores. Different sand granulations can be used to improve the surface quality.
5- REMOVING MOLD CORE
As with traditional production methods, the core and core of the mold cannot be reused.
6- AFTER THE PROCESS
It is processed after the part is removed from the mold. Casting parts prepared by 3D printing process significantly reduce the workload in subsequent processes. This is because even opposite angles and complex geometries can be printed as a single piece.