Sheet Forming Mold
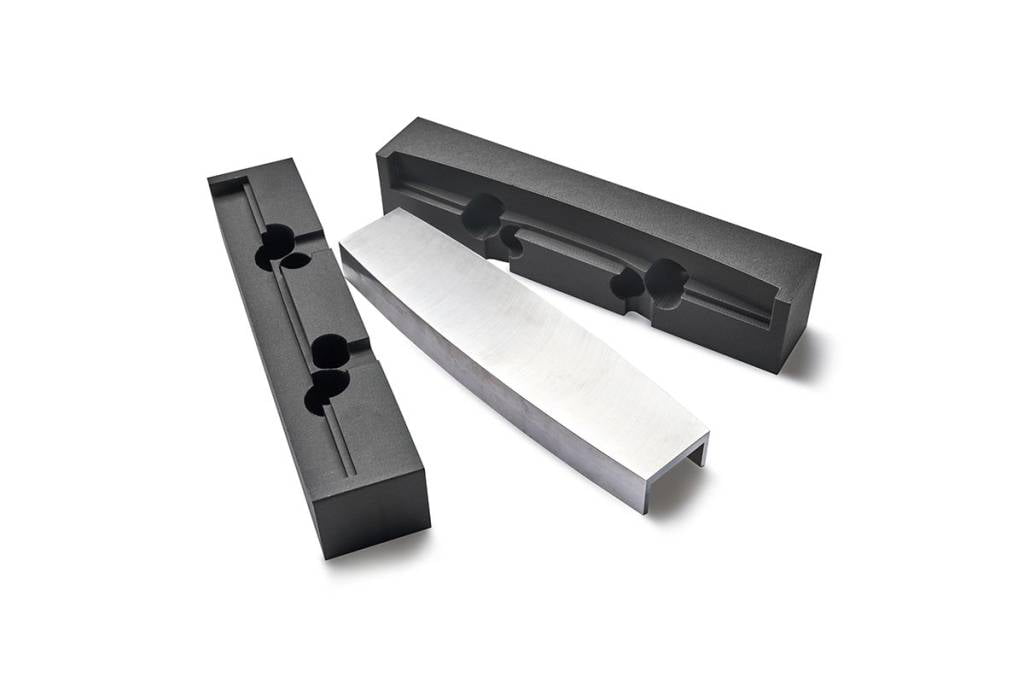
Hydroforming is the method of forming sheet metal parts, which is widely used for low volume part production in the aerospace and automotive industries. It is a method used for the production of new parts in the defense, aerospace and automotive industries, such as aircraft fuselage, engine components, suspension components, radiators, instrument panel support beams, to replace damaged parts on land or aircraft.
Sheet forming process takes place by taking aluminum, brass, carbon alloy steel or stainless steel sheet metals into the shape of the hydroforming mold with the help of high pressure.
Hydroforming molds are produced with CNC using traditional production methods. However, due to long delivery times and high costs for businesses, alternative mold production methods have been started to be researched.
As a solution, the production of sheet metal forming molds with FDM technology has taken its place in the industry over time and has yielded successful results. FDM is an alternative method that alleviates these challenges and helps companies move from vehicle design to production in as little as a week.
Contact Us for Your Offer Requests and Questions!
ADVANTAGES OF FDM TECHNOLOGY
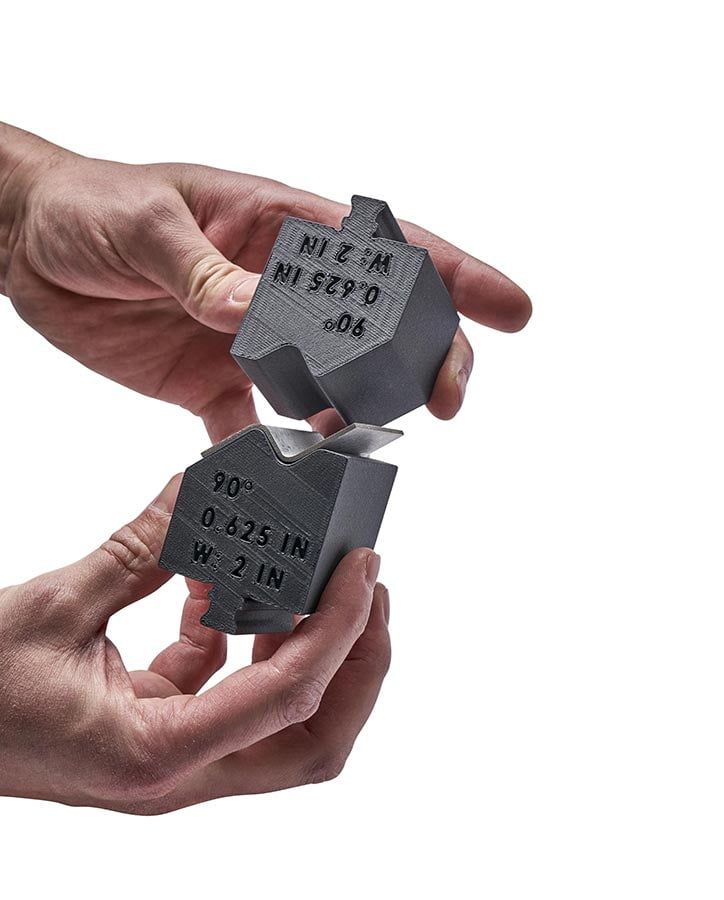
- Reduced Delivery Time and Costs: Depending on the geometry, sheet forming molds produced with FDM can be finished in less than 24 hours. It has seen 50% to 70% reduction in mold cost and 60% to 80% reduction in lead times compared to the traditional CNC manufacturing method.
- Design Flexibility: As it is possible to produce parts with complex geometry with FDM technology, you can develop your mold designs as you wish.
- Easy to Manufacture Direct from CAD Design: FDM is easy and fast to make design updates on your mold design from a digital CAD file. You can produce mold models with different designs in CAD environment according to your needs. In this way, you can avoid the producing spare molds and accumulating stock products problems and costly processes.
- Ergonomic Factors: Thermoplastic molds are generally much lighter than traditionally produced metal molds. With the design freedom you gain from FDM, you can produce and design lighter molds without sacrificing durability. This provides improved safety for machine operators by making molds more ergonomic than traditional tools.