Precision Casting Models
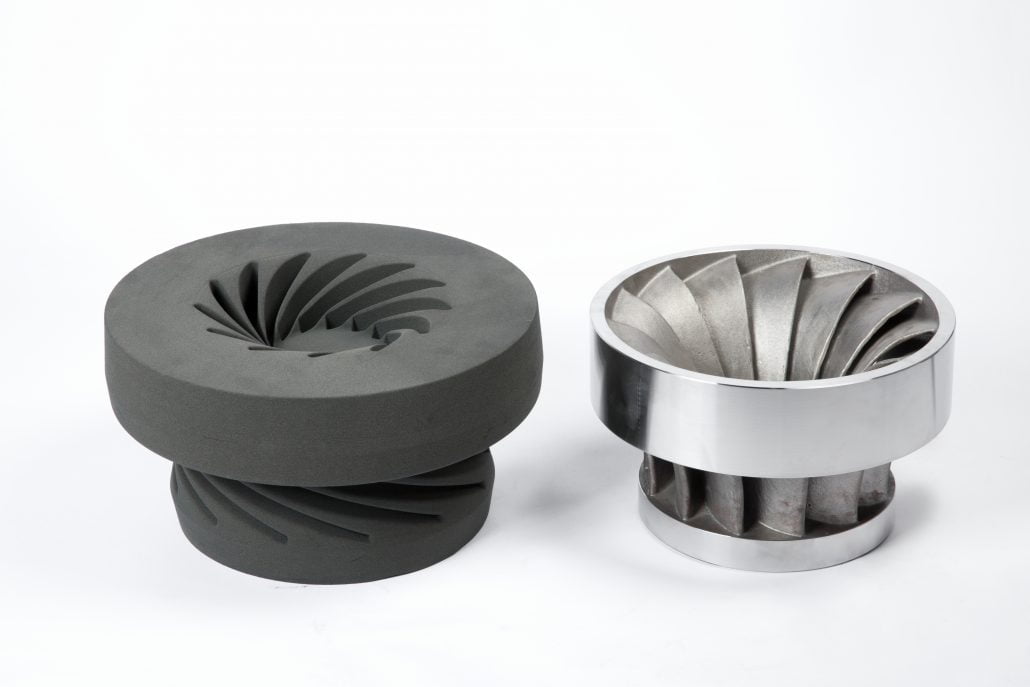
In order to produce a casting model with traditional production methods, an aluminum mold is usually produced and a mixture of plastic and wax models is produced by plastic injection method. Instead of such costly mold production and time-consuming processes, you can produce models with complex geometry thanks to 3D printing technology. You can not only depend on the geometry of the aluminum mold you produce, you can constantly produce models in different geometries and you can get rid of processes that take extra time and cost. With the 3D printing method, model parts are produced as a result of the binding of PMMA plastic powder particles, which are in a special binder and powder form. PMMA (polymethyl methacrylate), an acrylic plastic, is used as the model material and with sand molding technology, the models can go up to 1000 x 600 x 500 mm printing volume.
Contact Us for Your Offer Requests and Questions!
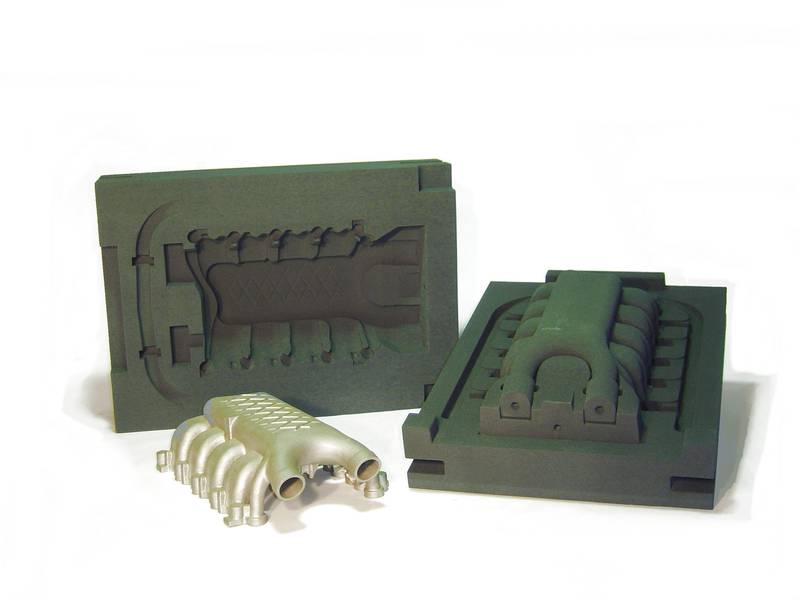
Beeswax material is a material that can melt at a temperature of 70-90 °C. It is also important that the model material has low thermal expansion property. Because the model is immersed in a ceramic bath (liquid plaster appearance) and covered with a thin layer around the model. This ceramic layer hardens in high temperature reheating furnaces and takes the geometric shape of the model. During this solidification period, the plastic and wax mixture model material under the ceramic shell is expected to flash without cracking the ceramic mold at the high furnace temperature. Then the ceramic mold is taken out of the furnace and the metal casting process takes place.
ADVANTAGES
Cost effective model production than traditional production methods.
It saves time in the process without the need for injection molding. The expensive injection mold production process is eliminated.
Thin elements with a wall thickness of up to 0.6 mm can be produced in the model geometry.
Possibility to produce a model with quality surface features thanks to its print resolution up to 600 dpi.
High dimensional accuracy casting can be performed without thermal expansion problem.
Surface coating can be applied with epoxy resin for smooth surface properties.
With its suitable flammable feature, without the thermal expansion problems that may arise from the furnace temperature and without cracking the ceramic shell, the model material burns and regains volatile properties.
The plastic powder material, which we call as loose powder and does not react with the binder during 3D printing, is an easy-to-use plastic material with 100% reusable feature for other productions.
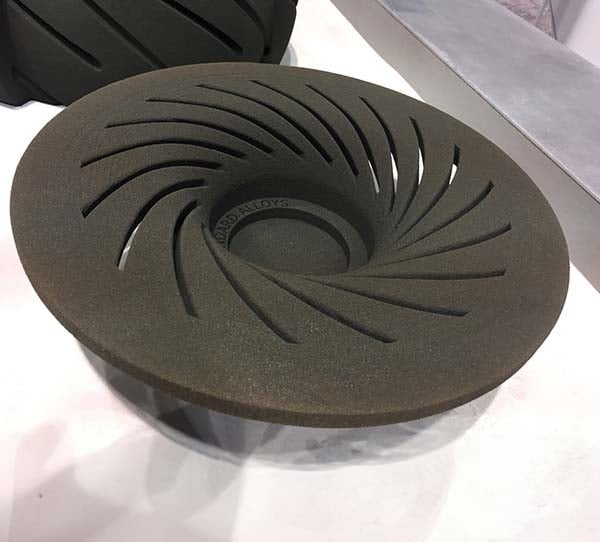
PLASTIC MATERIAL | ||
Model Material | PMMA powder (55pm particle size) | PMMA powder (85 um particle size) |
Binder Type | PolPor B (PPB) | PolyPor C (PPC) |
Tensile Strength: | ≥ 2.0 MPa | ≥ 2.0 MPa |
% Elongation (Yield Point) | one% | one% |
Burning Point: | 700 °C | 600 °C |
Residual Cinder Content | < % 0.01 | < % 0.01 |
Application area | Accurate casting model | Accurate casting model |
Advantages | Raw powders can be used again for production | High temperature volatile property is good |
CASTING MODEL | |
Layer Thickness | Standard 150 µm |
Surface Resolution x,y | 600 dpi |
Accuracy | ± 0.4 % (min. ± 0.3 mm) |
WAX (WAX) | EPOXY | |
Tensile Strength | ≥ 2.0 MPa | 25 MPa |
Softening Point | 73°C | 80°C |
Burning Point | 700°C | - |