Low Quantity Production
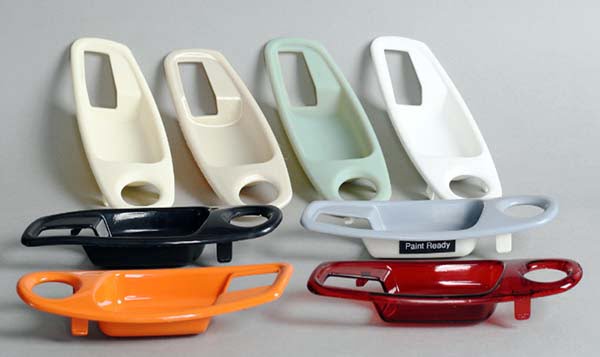
- In functional prototyping, which is the second phase of the product development process, we enable you to test the mechanisms that need to work with each other, from assembly interfaces to fit tolerances.
- The prototypes we produce with real engineering materials “ABS, PA, PU, PP, PC, ULTEM, Aluminum, Stainless Steel, …” are tested, their performance analyzed and presented to the user experience.
- Before your production lines are established, we can meet your functional product needs with our 3D Printer technologies.
- We offer many value added services for your functional parts.
Contact Us for Your Offer Requests and Questions!
APPLICATIONS
Manual operations such as tapping and threading by guide
Insert production and assembly
Turn and milling operations
Bonding, welding and different assembly operations
Surface applications such as polishing and sanding
Sealing operations
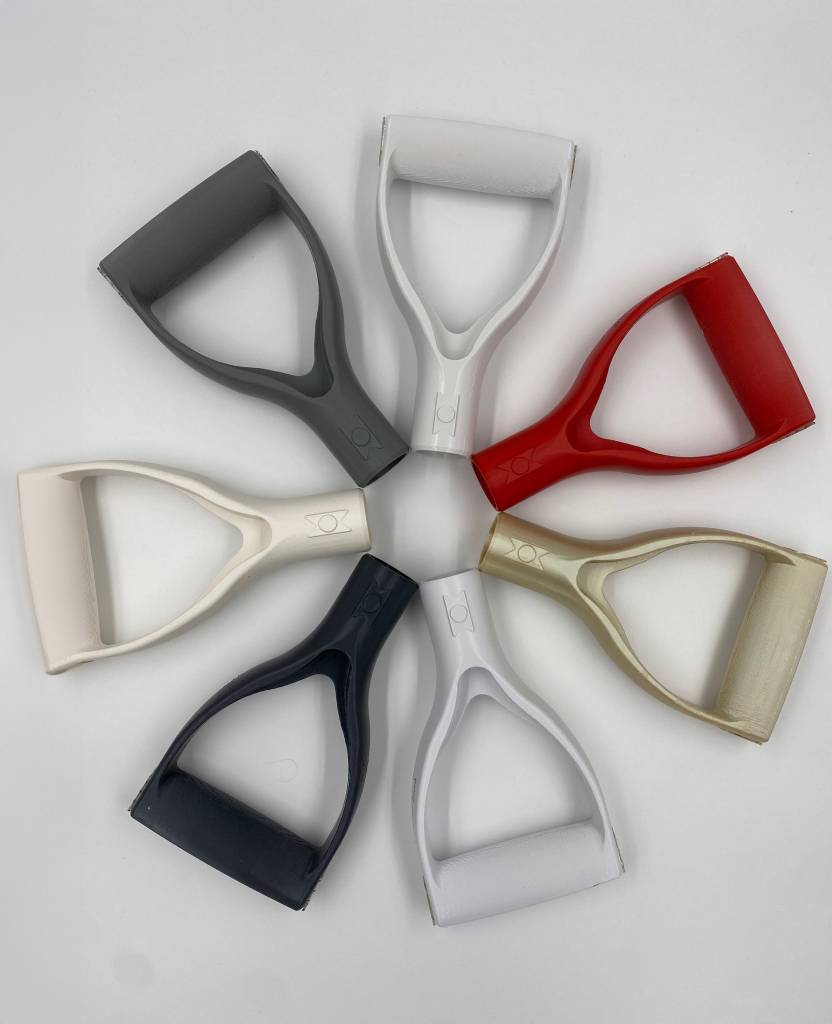
3D PRINTING TECHNOLOGIES IN LOW QUANTITY PRODUCTION
3D printing, which was designed for prototype production in the past, can be used today as both prototype production and the main manufacturing method. 3D printing process has the advantages of customization, design freedom and easy assembly. In addition, it enables low quantity production with low cost. Another benefit of 3D printing processes is that they are environmental friendly. Additive manufacturing methods have high efficiency and can reduce the amount of waste material by up to 90%.
The most costly and labor-intensive part of the product development process is mold production. 3D printing also reduces the need for mold production, reducing lead time, cost and labor required.
Traditional manufacturing methods such as injection molding are generally preferred for mass production. 3D printing is more economical than traditional manufacturing methods for low quantity production. It reshapes the product development and production process because it is fast and economical. Engineers and designers save time and cost by producing prototypes with 3D printing technologies. 3D printing has become an invaluable technology due to its ability to both save time and produce high accuracy models.
Molds produced with 3D printing reduce the standard injection molding process that takes weeks and months to hours and days. Small parts and functional, testable injection molds can be produced faster than ever before with 3D printing technologies. Molds produced with 3D printer technology can be tested to learn the values of impact resistance, chemical resistance, water tightness and flexibility when time is tight. Additive manufacturing is a fast and versatile technology as it can produce molds in less than a day.
If you want to produce less than 1000 pieces, 3D printing molds are the best manufacturing method for you. In manufacturing processes, especially in the production of plastic parts, the cost decreases as the number of parts increases. Injection molding is very expensive when the number of parts is low. In such cases, choosing 3D printing technologies offers you time and cost advantages.
Small parts with complex structures can be produced with high quality and high accuracy with 3D printing technologies. Parts can be produced with high quality engineering materials for the medical, aerospace and automotive industries.
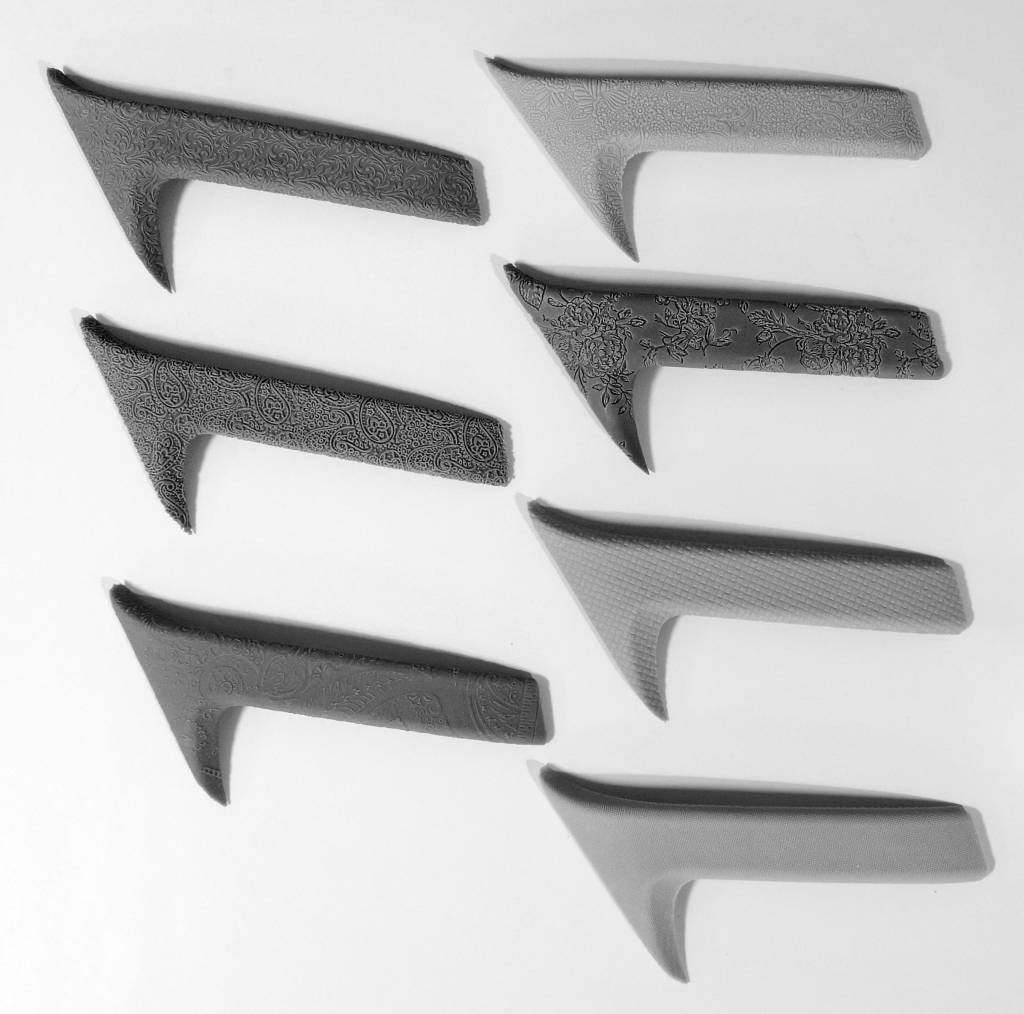
FAST MOLDING OR 3D PRINTING?
We have listed 7 important criteria you should consider in order to help you find an answer to your question, “Which production method should I choose for my low quantity parts needs?”.