Cooling Channel Mold
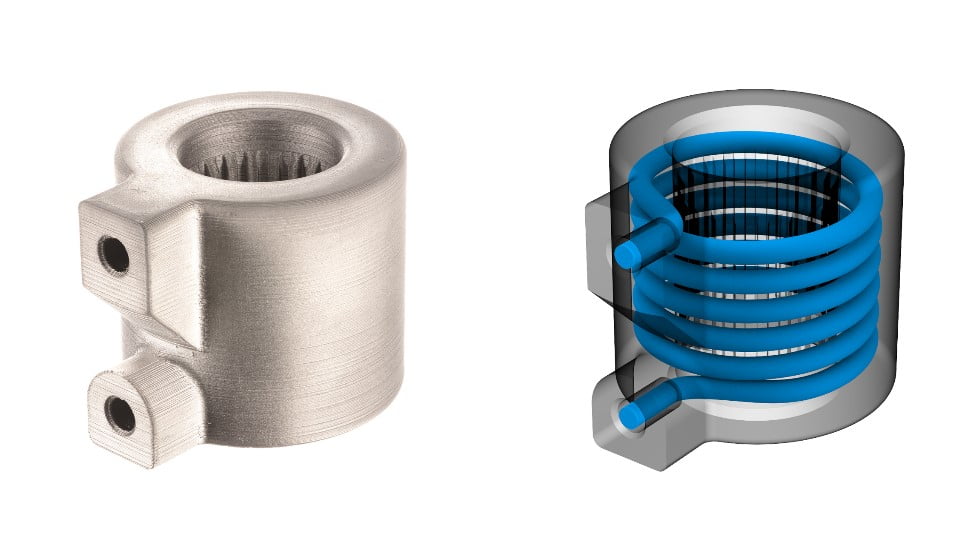
The cooling channel mold allows the plastic to be cooled faster, more balanced and therefore it makes higher quality, faster and more cost-effective production. Thanks to the freedom of design, mold geometry, which takes time to be produced with traditional methods, is made possible with metal additive manufacturing technology, and improvements can be made in the mold design of the geometry where the use of molds can be most efficient.
Two common examples of parts that require many channels in design are mold applications that require cooling and heat exchangers. For mold applications, internal cooling channels provide high performance features such as shorter cycle times and longer tool life. In heat exchangers, inner channels allow highly efficient designs with increased surface area, resulting in a much faster heat transfer.
In traditional production methods, complex inner channels are usually formed by molding or machining two parts and combining them by frequent welding to form a closed inner channel.
Contact Us for Your Offer Requests and Questions!
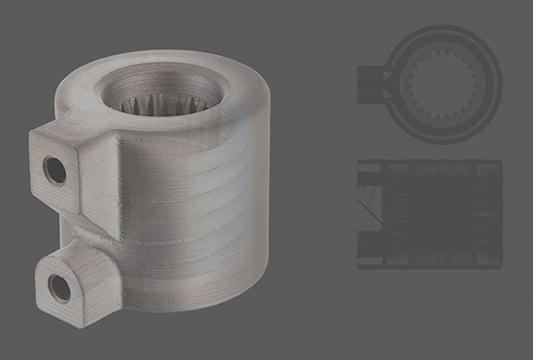
Additive manufacturing technology ensures that internal channels are properly included directly in part design and significantly reduces manufacturing complexity (additional processes such as welding, assembly, etc.). Thanks to the freedom of design, it offers possibilities such as conformal cooling channels with complex structure and special manifolds.
You can see the comparison of cooling channel molds produced with traditional production and 3D Printing Technology in terms of design. Traditional cooling channels are shown on the left; suitable cooling channels are shown in the right picture.