From a coin to a fighter jet!
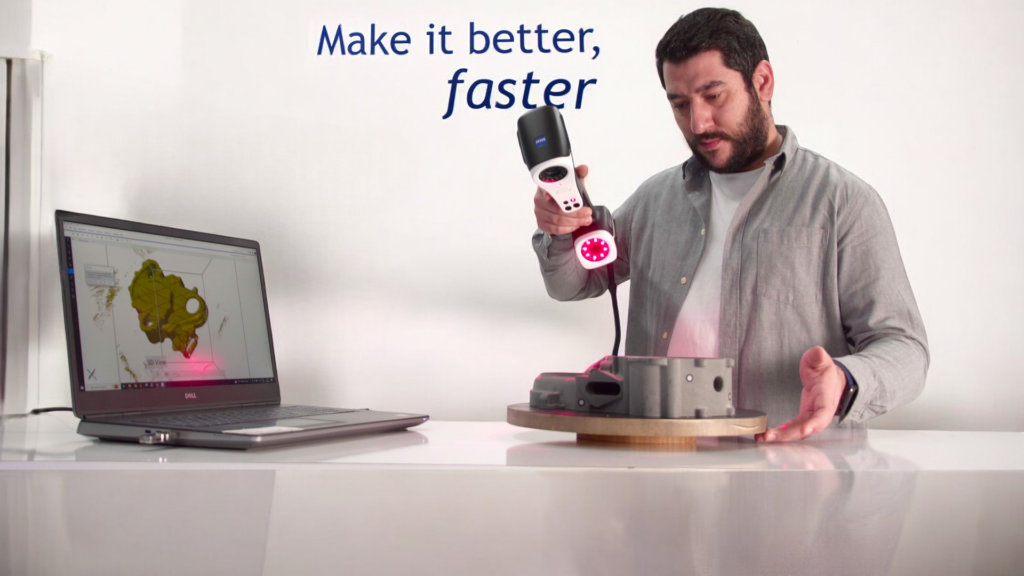
3D SCANNING
We can scan any product, from a coin to a fighter jet, with our industrial scanning systems and perform modelling, reverse engineering and 3D quality control.
3D scanning is the fast, consistent and easy creation of a 3D representation of a tangible object for the computer environment. In other words, 3D scanning; It is the first step taken to create CAD data for a part that does not have 3D CAD data.
Object data obtained by 3D scanning is adapted using special software for quality control and reverse engineering applications, according to the customer’s request, or is delivered to the customer in formats such as STL, OBJ without any additional processing.
As +90 3D Digital Factory, we can perform 3D scanning of objects of different sizes, from a pin to a factory, with the different lens heads we have.
Contact Us for Your Offer Requests and Questions!
3D Scanning
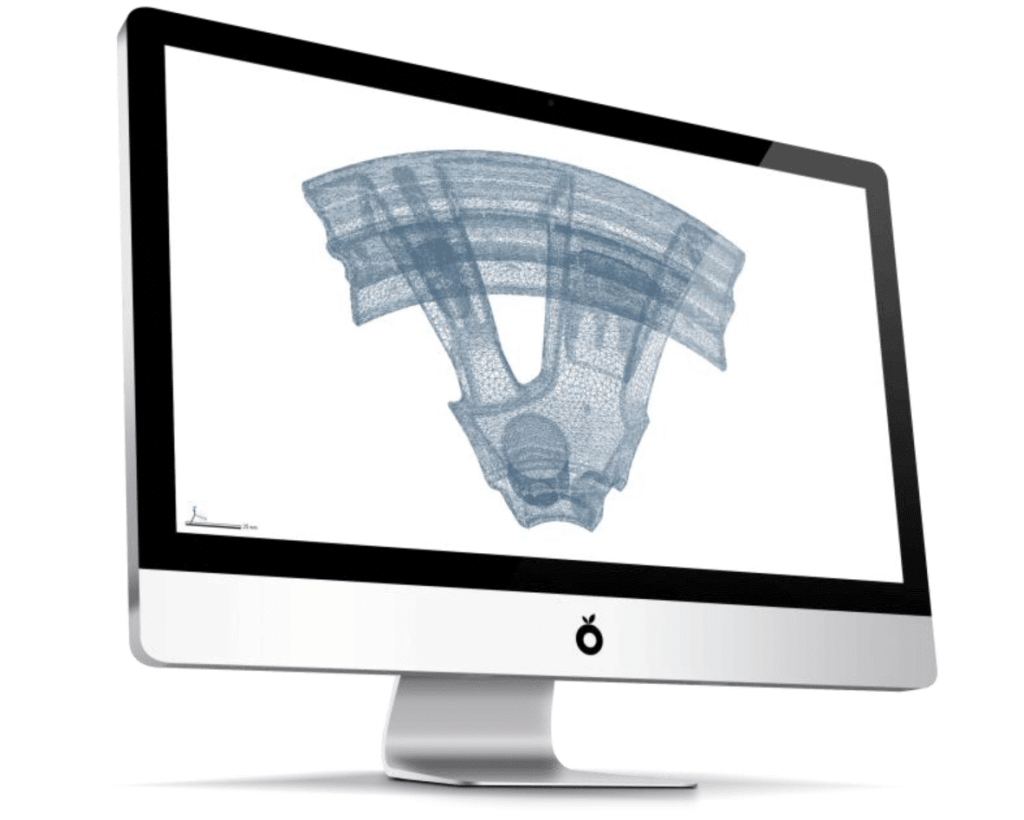
3D Modeling
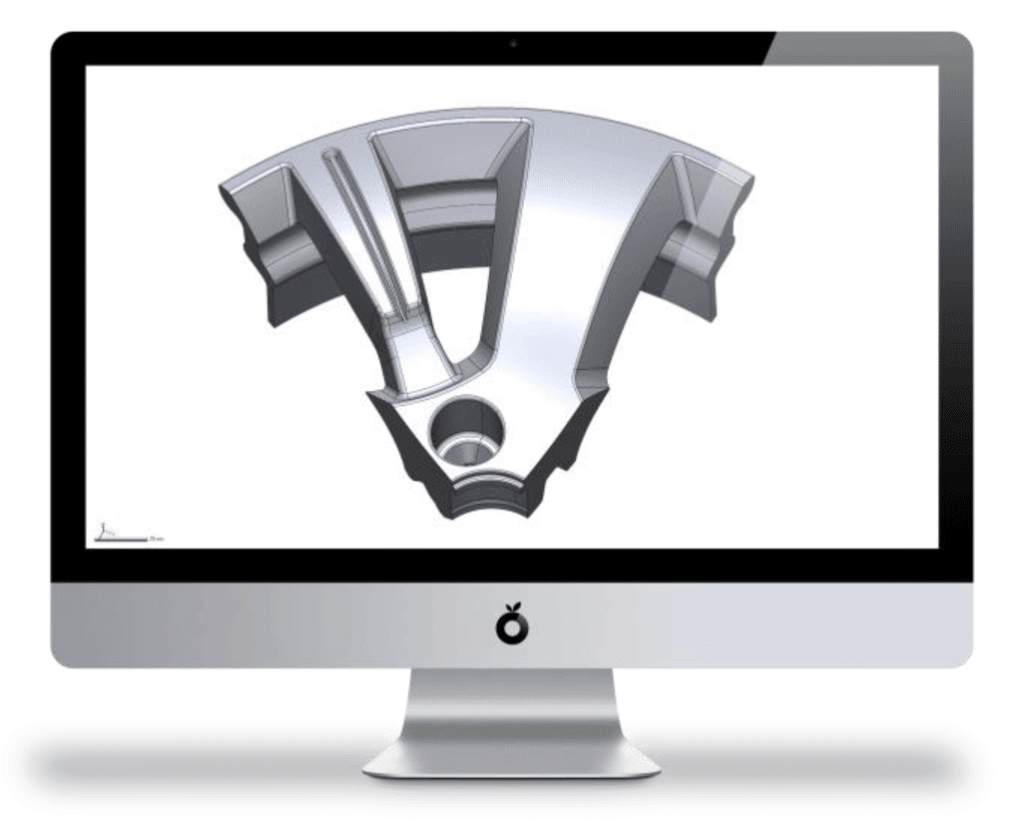
3D Quality Control
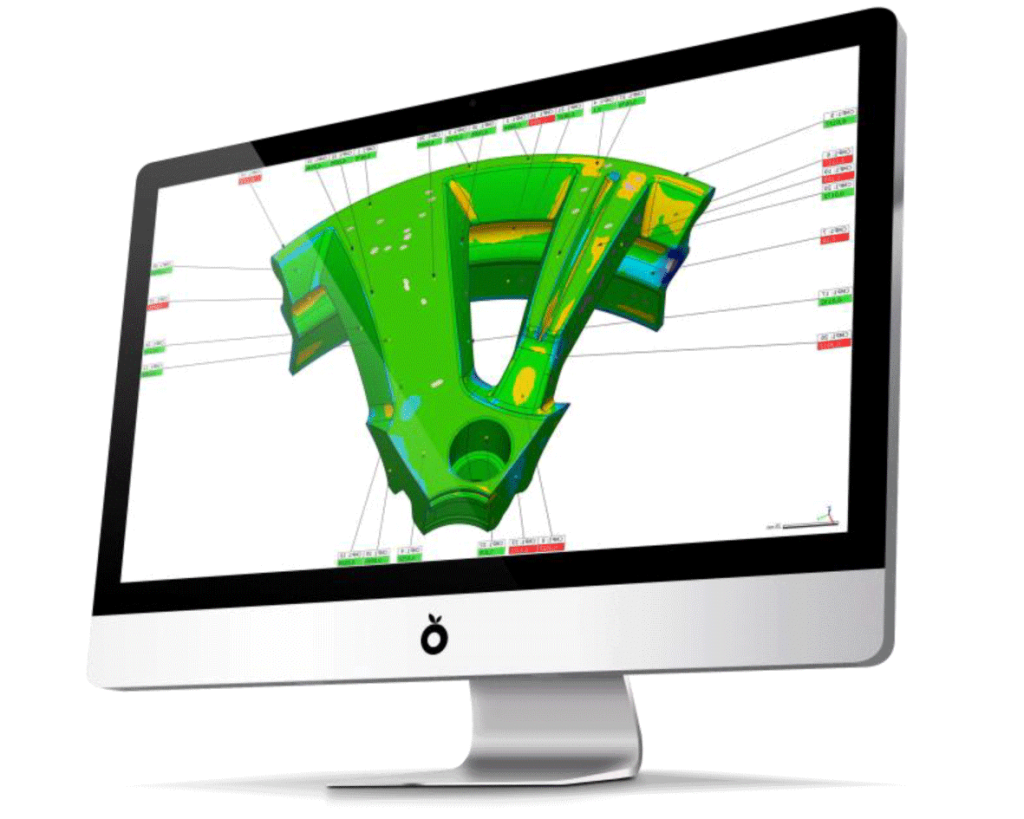
PROBLEMS YOU CAN SOLVE WITH 3D SCANNING
- Lack of 3D data of the product to be reproduced
- The original design had insufficient documentation
- The product the customer needs is no longer produced
- Analysis of the good and bad features of the competitor product
- Need for revision in product design
- Original CAD data is not sufficient for current manufacturing methods
- Deterioration control in working parts
[email protected]
The object for which 3D data is to be created is scanned with optical scanners. While cameras with two sensors continuously record the process, projector beams are moved over the object with special software. Cameras record distance and shape changes in 3D on the XYZ axis as the projector beams move over the object. As the rays move to capture all surfaces of the object, they are displayed on the computer screen as millions of points called a “point cloud”. The data collection process is very fast and takes 750,000 points per second.
Once point cloud data is obtained, it is saved and combined to create a 3D representation of the object. The obtained 3D data of the object is made ready for quality control or reverse engineering applications using various software.
The data obtained by 3D scanning is used to compare with the main design data in quality control applications. The comparison results of scanning data and CAD data are delivered to the customer as a deviation report shown with a color scale.
Optical scanning is the fastest and most accurate method that can be used to obtain 3D data of an object for reverse engineering applications. The point cloud of the part, together with specialized software, is used to create a 3D model of the part’s geometric shape. The 3D model is used to reproduce the scanned object with high accuracy or to correct errors by making changes to the model.